The realm of 3D printing technology is continually evolving, presenting groundbreaking solutions in various industries. One of the most exciting developments is the collaboration between Linde and the Ariane Group, which aims to enhance the 3D printing of copper alloys for rocket combustion chambers. This partnership is not just a leap in additive manufacturing but a testament to how technology can revolutionize aerospace engineering.
Understanding the Challenge with Copper in 3D Printing
Copper alloys are crucial in aerospace for their high thermal conductivity, making them ideal for components like rocket combustion chambers. However, the very nature of copper poses a unique challenge in 3D printing, specifically in laser powder bed fusion (LPBF) processes. The primary obstacle is copper’s high reflectivity to laser beams, which can cause issues such as inefficient melting, overheating, and oxidation of the parts being printed.
The Issue of Overheating and Reflectivity
In traditional 3D printing processes, copper’s reflectiveness to laser beams necessitates higher laser intensities. This approach, however, raises significant concerns regarding part overheating and oxidation – two factors detrimental to the quality and reliability of aerospace components.
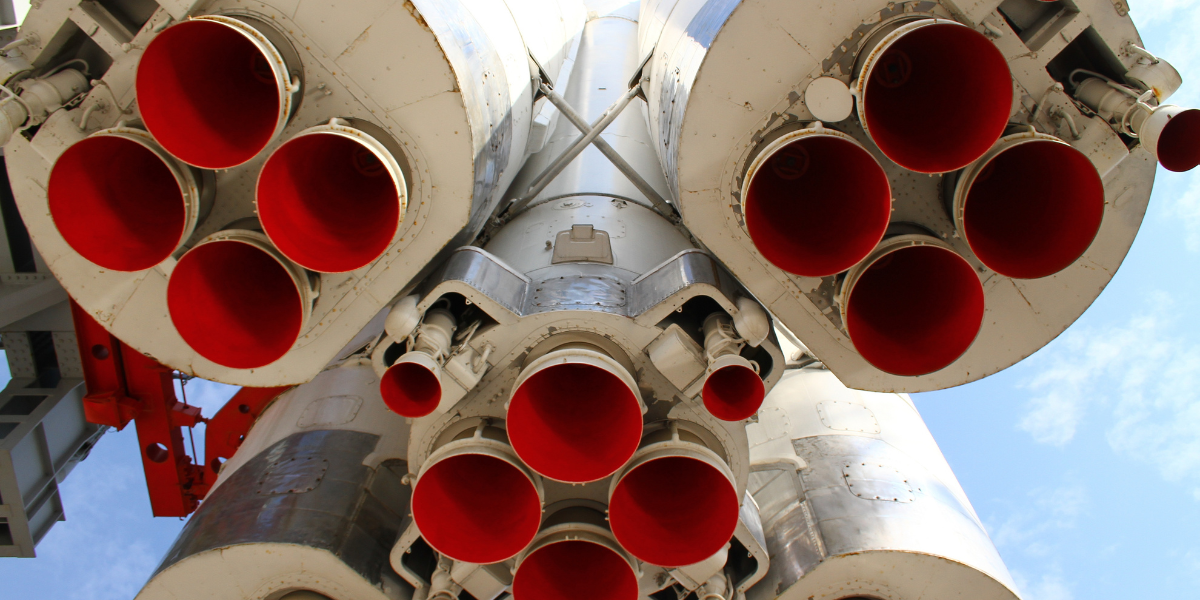
Linde’s Innovative Solutions: ADDvance Laser230 and O2 Precision
ADDvance Laser230: Enhancing Efficiency and Reducing Costs
Linde’s response to these challenges is the development of ADDvance Laser230, a specialized gas mixture tailored for LPBF processes. This innovative solution effectively reduces the problems associated with fumes and spatter during the printing process. Moreover, it optimizes cycle times, thereby enhancing the overall reliability of the printing process and reducing the costs per part.
ADDvance O2 Precision: Maintaining Optimal Oxygen Levels
Complementing the Laser230, Linde introduced the ADDvance O2 precision system. This technology plays a crucial role in refining the printing process by maintaining oxygen levels within the print chamber at a minimal 10ppm. This precision control prevents oxidation and overheating, allowing for continuous printing without the need for cooling intervals. Additionally, it enables the reuse of non-oxidized powder, further lowering material costs.
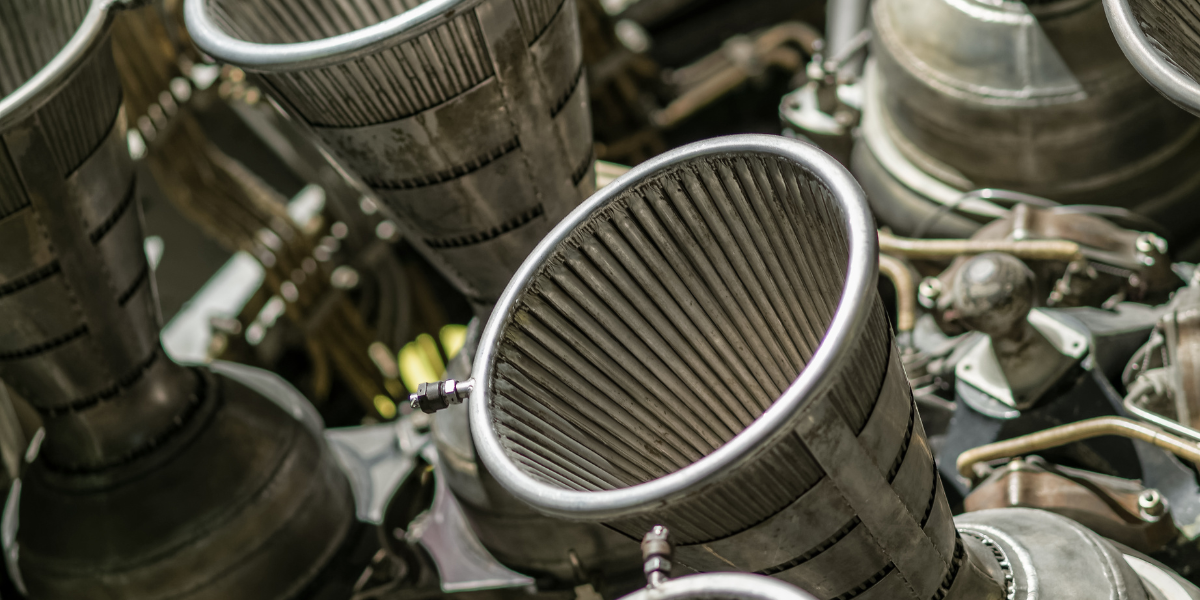
The Future of Aerospace Manufacturing with 3D Printing
Transforming Industry Approaches
The advancements made by Linde and the Ariane Group are about more than just overcoming the challenges of using copper in 3D printing. They represent a significant shift in how the aerospace industry approaches the manufacturing of critical engine parts. The potential for more efficient production of high-performance aerospace components at reduced costs is immense.
The Role of Gas-Mixing Technologies
The future of aerospace engineering could be heavily influenced by gas-mixing technologies like those developed by Linde. These technologies can potentially become a standard in manufacturing high-end aerospace components, offering benefits such as increased efficiency, reduced production costs, and improved part quality.
The collaboration between Linde and the Ariane Group marks a significant milestone in the field of 3D printing technology. By addressing the unique challenges of printing with copper alloys, they are paving the way for more advanced, efficient, and cost-effective manufacturing methods in aerospace engineering. This partnership not only highlights the potential of 3D printing in transforming industries but also underlines the importance of continuous innovation in technology for future advancements.